Greystones’ approach to quality assurance is derived from our implementation of ISO 9001:2015, the Carnegie Mellon’s Capability Maturity Model, and the Seaport-e contract requirements. This provides us the best assurance of consistently delivering quality products on time. Greystones, not the government, is solely responsible for implementing and maintaining the appropriate controls to produce and assure the quality of service required by our contracts.
Quality Assurance
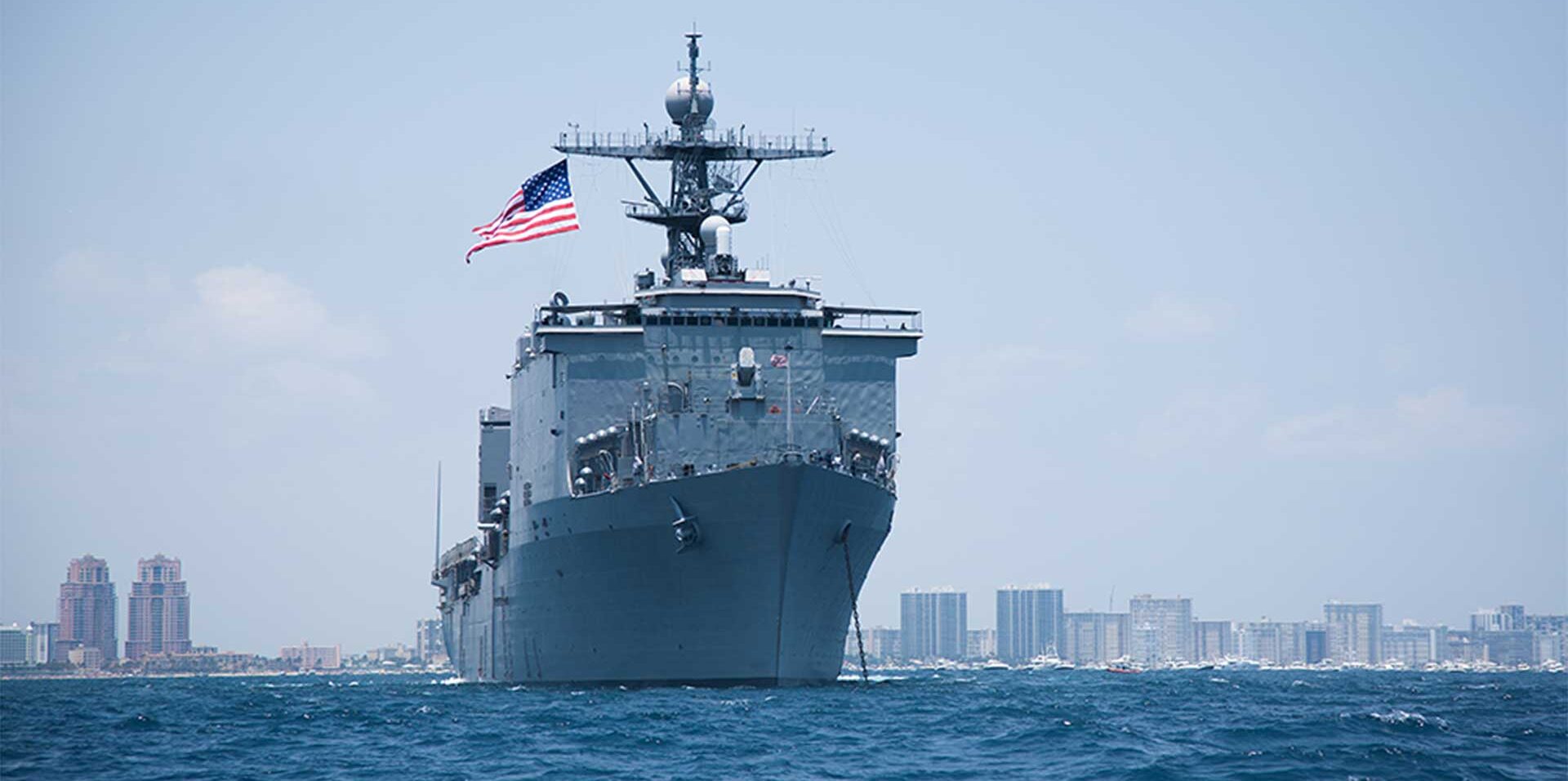
Establishing uncompromising excellence.
Greystones provides total client satisfaction through effective program execution, process improvement, and implementation of best practices.
We provide provisions for the following:
- Quality Control (QC) inspections
- Quality Control Inspectors for both the procedures and corrective processes
- Management team responsibilities regarding quality control processes
- A process for identifying, reporting, correcting, and tracking deficiencies
- A customer complaint feedback system
- Written and verbal communications with the government
- Means for identifying unsatisfactory performance and correcting deficiencies
- Surveillance techniques and a schedule to monitor performance
Planning.
Our documented Quality Assurance Plan includes sets of repeatable processes and associated checklists ensuring that all critical functions are performed for each task. The term “repeatable processes” does not imply that tasks are not tailored, rather that many tasks can be grouped into a standard process that includes specification. Once the Greystones Team Program Manager is authorized to interface directly with the technical point of contact and other NAVSEA personnel, we enter the planning phase.
Planning actions required to initiate a task include:
- The estimates of cost to perform
- The assignment of the technical point of contact for the task
- The start date
- The required delivery date
- The content, form and format of the deliverable itself, and
- The designated recipient of the final deliverable
Execution.
The execution phase of our task is controlled through standardized and documented procedures that contain the step-by-step processes required to perform contract tasks. These procedures form the basis for measuring performance, and for ongoing training of the Greystones team. Throughout the execution phase, the Management IPT and the Technical IPTs meet frequently to review progress and adjust standard processes to correct any deficiencies found during quality checks.
Monitoring and Controlling.
All products are checked for form, format, and technical content during periodic scheduled and unscheduled checkpoints. A third party QA check is required to verify that the procedure has been followed correctly up until that point. Both the person executing the procedure and the person conducting the independent QA check must be certified to perform the specific procedure. A matrix in the defined repeatable process identifies these qualifications. Our training plan uses this matrix to schedule additional training to increase certification and cross training of personnel across all processes.
Monthly formal reports are also provided in compliance with the typical reporting requirements of most tasks. The monthly report includes a complete technical status of the task in process, if required, and the cost and labor hours expended to date.
Delivery.
Before delivering the finished product, a qualified senior person checks it for form, format and technical content. Once delivered, Greystones requires the receiver to both approve our product and assess our performance at the time of delivery. This allows us to improve our future performances and maintain an unparalleled level of quality assurance.